twin roll press
Construction of twin roll press
Twin roll press is a new type of high efficiency equipment for extracting pulp black liquor and washing and concentrating. It is mainly made up of tank body, middle bottom, press roller, spray device, longitudinal seal device, end seal, scraper device, crushing screw conveyor, machine cover, motor and hydraulic station, etc.
Tank body
The tank body is a steel plate welding structure, its function is to support and hold the material. The bearing seat of the moving roll and fixed roll is installed in the wall board on both sides of the tank.
Rise and fall bottom
The middle bottom shall be connected with the tank body by bolts, and the contact surface with the tank body shall be straight and smooth. Through the action of two lifting cylinders, the midsole can conveniently and quickly clean the residual slurry inside the tank body, replace the sealing elements, and maintain the equipment.
Press rolls
The press roller is a roller with a latticed structure. The surface of the roller is equipped with a perforated filter plate. The lower part of the filter plate is divided into a uniform bin with open structure at the two ends of each bin, so that the filtrate entering the filter plate can be discharged smoothly out of the roller. There are fixed and moving rollers in the press roll. The gap between the two rollers and the linear pressure can be adjusted so as to prevent the two rollers from being damaged by overpressure.
Longitudinal sealing device
Longitudinal sealing device is divided into static sealing device and dynamic sealing device, which are located on the side of fixed roller and moving roller respectively. Sealing scraper material is made of PTFE plate, the power is realized by sealing gas.
End seal
The end seal is located at the two ends of the roller. The purpose of the seal is to separate the slurry in the tank from the filtered black liquor, which is mainly composed of two semi-rings of the sealing ring and the seal seat. The sealing ring is pushed to the ring plate at both ends of the roller by air pressure. Ensure that the slurry in the tank does not leak out.
Scraper device
Scraper device is divided into static scraper device and dynamic scraper device, located on the top of the roller, both sides of the discharge screw, its function is to scrape the slurry layer on the surface of the roller and to play the sealing function, and the scraper is made of polytetrafluoroethylene (PTFE). The static scraper is located on the side of the fixed roller, and the moving blade is located on the side of the moving roller, which can be moved with the roller.
Broken screw conveyor
The screw conveyor is located at the upper part of the two rollers and consists of a shell, a helical shaft, a transmission, etc. The helical blade on the helical shaft is composed of two parts, and the edge of the blade at the upper part of the two rollers is zigzagged. In order to transport at the same time effectively the high concentration of the pulp into pieces, two-roll blade for the conveyer blade.
A machine mask
The hood is made of fiberglass and has an inspection hole. There is an exhaust port at both ends of the hood. The gas in the hood can be discharged from the machine through the exhaust fan.
After-sales service commitment
- Provide relevant technical consultation, technical cooperation, technical training and other process services in time for engineering installation, commissioning, acceptance, operation, maintenance and so on.
- Provide technical information and drawings for engineering design in time.Timely send technical personnel to the site to cooperate with the buyer according to technical materials and drawings to guide the assembly and commissioning.
- Provide life-long maintenance consulting service under normal use. Investigate the use of the equipment every 6 months, and make recommendations to the user on the operation and use of the equipment in time, and make a better use standard for the use of the equipment.
Advantages
- Adopting international advanced hydraulic drive system, pulp distributing system and washing system.
- With washing, dewatering and displacing equipments.
- Fully improved pulp feeding structure designed with independent intellectual property rights to get better distributing effects.
- Brand-new sealing and scraping mechanisms with good sealing in operation and convenience in control.
- Larger filtration area and stronger displacement performance to get better pulp washing effects.
- Advanced Sweden hydraulic drive system with more stable and liable performances.
- More modern control system for remote control.
Construction A/B
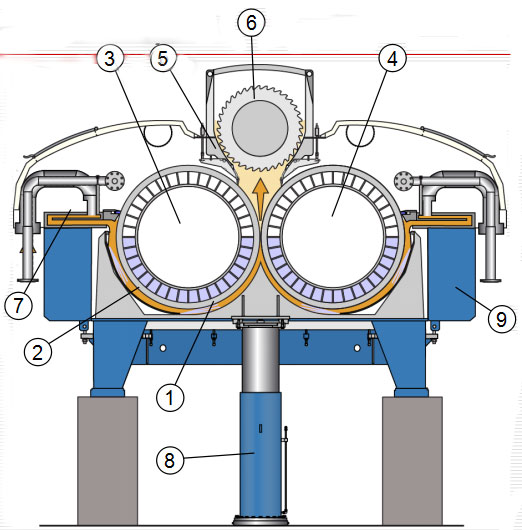
1.Central part 2.Sliding plates 3.“Fixed” roll 4.“Movable” roll 5.Doctors 6.Pre-breaker 7.Frame 8.Telescopic column 9.Frame
Technical parameters
Model /Item | Drum length (mm) | Drum Dia. (mm) | Drum Speed (rpm) | Feed Consistency(%) | Discharge Consistency (%) | Production Capacity | ||
Straw / Bagasse pulp | Bamboo pulp | Wood pulp | ||||||
AMSG712 | 1200 | 700 | 2~20 | 3.5~10 | 20~35 | 30~40 | 60~80 | 80~100 |
AMSG915 | 1550 | 900 | 2~15 | 3.5~10 | 20~35 | 40~60 | 85~120 | 130~160 |
AMSG920 | 2000 | 900 | 2~15 | 3.5~10 | 20~35 | 55~85 | 125~160 | 175~210 |
AMSG928 | 2820 | 900 | 2~15 | 3.5~10 | 20~35 | 80~120 | 165~220 | 250~300 |
AMSG935 | 3500 | 900 | 2~15 | 3.5~10 | 20~35 | 110~150 | 225~280 | 310~370 |
AMSG940 | 4000 | 900 | 2~15 | 3.5~10 | 20~35 | 120~170 | 220~310 | 350~400 |
AMSG945 | 4500 | 900 | 2~15 | 3.5~10 | 20~35 | 160~180 | 285~350 | 400~480 |
AMSG1532 | 3200 | 1500 | 2~15 | 3.5~10 | 20~35 | 220~350 | 450~600 | 700~800 |
AMSG1540 | 4000 | 1500 | 2~15 | 3.5~10 | 20~35 | 400~550 | 800~1000 | 1200~1500 |
AMSG1550 | 5000 | 1500 | 2~15 | 3.5~10 | 20~35 | 500~650 | 1000~1300 | 1700~1800 |
AMSG1572 | 7200 | 1500 | 2~15 | 3.5~10 | 20~35 | 750~1000 | 1500~1800 | 2500~3000 |