A patent about pulping purification equipment with a suspension tank
Introduction of the pulping purification equipment
Nowadays, some people in China apply for a patent about waste paper pulp purification equipment with a suspension tank. This patent solves the problem of purification on the efficiency and quality of waste water treatment. When processing the waste paper into pulp, generally, the paper is directly crushed and then water is added to the pulp mixing operation. Finally, the mixed pulp water is screened and concentrated. After a certain period of store time for the waste paper, some impurities will remain on the surface. Although the larger impurities are separated during the crushing and screening work, many lighter impurities, such as the cotton wool and wood chips that adhere to the surface of the waste paper with residual glue, will still have residues and float in the slurry. Although these residual impurities can be separated and discharged together with the wastewater in the process of fiber separation after compression in the subsequent process, these impurities are mixed in the discharged wastewater, which will increase the time of dealing with waste water with purification equipment and increase the purification burden.
1-box body 2-the first motor 3-connecting rod 4-first stirring rod 5-guide plate 6-solenoid valve 7-baffle 8-the second motor 9-second stirring rod 10-heating equipment 11-placement box 12-installation block 13-installation rack 14-flow channel 15-connector 17-cleaning plate 18-anti-off board 19-attached layer 20-push block 21-sliding panel 22-dewatering screening device 23-suspension purification device 24-water pump
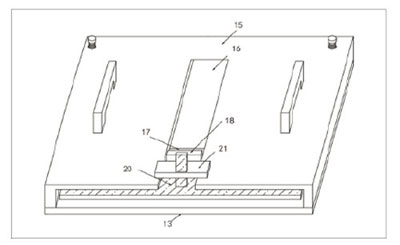
Structure of mounting frame and connecting frame

Planform of placement box
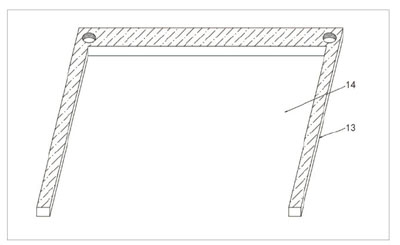
Stereoscopic diagramme of mounting frame
Configuration of pulping purification equipment
Just as the pictures above, this pulping purification equipment contains a box body, a dehydration screening device and a suspension purification device. They are connected to each other.on the body, there connects the first motor, and the output end of the motor penetrates the box,then the first motor is electrically connected to the external power supply, and the end of the first motor is connected with a connecting rod, which has some first stirring rods under it.
The inner wall of the box body is fixedly connected with a baffle, the center of the baffle is provided with a solenoid valve, the outer wall of the box body is fixedly connected with a second motor, and the output end of the second motor is fixedly connected with a number of second stirring rods, and a suspension purification device. A placement box is fixedly connected to the upper end of the suspension purification device, two symmetrically distributed mounting blocks are fixedly connected to the inner wall of the placement box.
Working principle of pulping purification equipment
Before mixing the pulp, put the broken paper and water into the storage box for a preliminary precipitation. After the broken paper is completely settled, through the push block to drive the cleaning plate to move, so that the cleaning plate move the impurities floating on the water surface to one side, until the cleaning plate touches the inner wall of the connecting frame. Impurities are blocked between the connecting frame and the cleaning plate, so that when the settled paper and water enter the box through the pumping of the water pump, the impurities remaining between the connecting frame and the cleaning plate are blocked by the connecting frame and the cleaning plate. It will not flow with the shredded paper and water, thereby reducing the possibility of floating impurities entering the box, so that these impurities will not be mixed in the discharged waste water during subsequent filtration and water treatment.
When the material enters the inside of the box, it will be blocked by the baffle and the solenoid valve in the center. At this time, the first agitating rod is driven by the first motor to initially agitate the paper and water into a slurry. The output of the first motor has a fixed rod, and the length of the six first agitating rods is reduced by 10cm from right to left, so that the first agitating rod will not be blocked by the baffle when rotating, so that the mixing surface of the slurry is wider and more sufficient. After the initial slurry is stirred, the solenoid valve is energized, and the material is guided by the two guide plates and flows into the bottom of the baffle through the solenoid valve. At this time, the heating device is turned on to heat the slurry flowing down, so that the slurry reaches the required temperature, and then use the second agitating rod of the second motor to perform secondary mixing, and there is no need to transfer the material during the two mixing work, which is more consistent and occupies less space, allowing the material to pass through the vertical stir evenly in the vertical and horizontal directions twice to improve the pulping effect of the pulp.
There is a pipeline connected between the bottom of the box and the dewatering and screening device, and there is a water valve on the pipeline. After the pulp is pulped, the water valve is opened to allow the slurry in the box to flow into the dewatering and screening device for dehydration and concentration. It is discharged from the discharge end, and the waste water flows into the suspension purification device through a drainage pipe, and is purified by the suspension purification device to complete the recovery of the waste water. After completion, the connecting frame and the mounting frame are pulled out from the upper ends of the two mounting blocks. After that, disassemble the mounting frame and the connecting frame, loosen the bolts and take out. After disassembly, the impurities between the connecting frame and the cleaning plate can be cleaned, and the next use can be done after cleaning. The connecting frame is provided with a sliding groove, the upper end of the cleaning plate is fixedly connected with an anti-falling plate, the anti-falling plate is slidingly connected with the sliding groove, and the pushing block is fixedly connected with a sliding plate. The width of the sliding plate is greater than that of the sliding groove.
Here is the specification of our vacuum drum washer, this equipment is necessary during the pulp washing.
Model /Item | Drum length (mm) | Drum Dia. (mm) | Drum speed (rpm) | Feed Consistency(%) | Discharge Consistency(%) | Capacity( black liquor extraction)(Kt/m2.d) | ||
Straw /Bagasse pulp | Bamboo pulp | Wood pulp | ||||||
AMXJ35 | 3200 | 3500 | 0.8~3 | 1.5~2.5 | 8~12 | 52.5~87.5 | 175~210 | 210~280 |
AMXJ40 | 3650 | 3500 | 0.8~3 | 1.5~2.5 | 8~12 | 60~100 | 200~240 | 240~320 |
AMXJ45 | 4100 | 3500 | 0.8~3 | 1.5~2.5 | 8~12 | 67.5~112 | 225~270 | 270~360 |
AMXJ50 | 4550 | 3500 | 0.8~3 | 1.5~2.5 | 8~12 | 75~125 | 250~300 | 300~400 |
AMXJ55 | 5000 | 3500 | 0.8~3 | 1.5~2.5 | 8~12 | 82~137.5 | 275~330 | 330~440 |
AMXJ60 | 5450 | 3500 | 0.8~3 | 1.5~2.5 | 8~12 | 90~150 | 300~360 | 360~480 |
AMXJ65 | 5200 | 4000 | 0.8~3 | 1.5~2.5 | 8~12 | 98~162.5 | 325~390 | 390~520 |
AMXJ70 | 5600 | 4000 | 0.8~3 | 1.5~2.5 | 8~12 | 105~175 | 350~420 | 420~560 |
AMXJ75 | 6000 | 4000 | 0.8~3 | 1.5~2.5 | 8~12 | 113~187.5 | 375~450 | 450~600 |
AMXJ80 | 6400 | 4000 | 0.8~3 | 1.5~2.5 | 8~12 | 120~200 | 400~480 | 480~640 |
AMXJ85 | 6800 | 4000 | 0.8~3 | 1.5~2.5 | 8~12 | 127~212.5 | 425~510 | 510~680 |
AMXJ90 | 7200 | 4000 | 0.8~3 | 1.5~2.5 | 8~12 | 135~225 | 450~540 | 540~720 |
AMXJ95 | 7600 | 4000 | 0.8~3 | 1.5~2.5 | 8~12 | 143~237.5 | 475~570 | 570~760 |
AMXJ100 | 8000 | 4000 | 0.8~3 | 1.5~2.5 | 8~12 | 150~250 | 500~600 | 600~800 |
AMXJ105 | 7450 | 4500 | 0.8~3 | 1.5~2.5 | 8~12 | 157~262.5 | 252~630 | 630~840 |
AMXJ110 | 7800 | 4500 | 0.8~3 | 1.5~2.5 | 8~12 | 165~275 | 550~660 | 660~880 |
AMXJ115 | 8150 | 4500 | 0.8~3 | 1.5~2.5 | 8~12 | 173~287.5 | 575~690 | 690~920 |
AMXJ120 | 8500 | 4500 | 0.8~3 | 1.5~2.5 | 8~12 | 180~300 | 600~720 | 720~960 |